John_7951
New Member
Hi, I'm in the planning stages for remodeling my family room in the half-basement. I want to create an in-law suite including a barrier free bathroom/shower and a furnace room. This is following a major renovation and room addition in the rest of the house. Following construction, the original family room, utility room and power room were, essentially, trashed - but I expected that. I planned to finish this part of the house as "phase 2".
The original power room was pretty useless. I want to build a new bath with a roll-in shower & linear drain. The laundry was relocated to an upper level but I want to anticipate putting in a stackable washer/dryer in the new bathroom. Two furnaces were put side-by-side in the basement. They are loud and I need to enclose them.
The construction that supported the first renovation pretty much used the basement without much thought. One result is that the DWV and supply lines for the floor above consumed a lot of head room that I would like to get back. I also need to relocate the water heater to put a water softener in where I want it.
Right now, I'm just planning things out. I think I have a workable plan, but that remains to be seen. I need to do some prep work first to get things situated better before any real construction can begin.
So ... I will have a bunch of questions ...
To start this off, I want to upload some design pictures and then deal with a couple specific DWV rework efforts to help me get my head room back in the proposed location for the new bath.
Here's what the basement looks like now and my proposed designs.
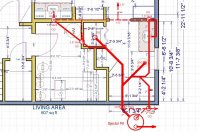
Here is the first question on re-working the DWV ... Can I move the drain pipe for the upstairs bathroom that runs overhead, across & under the joists? I want to route it so it ties into another stack that is next to the furnace. Please see these photos in the next post ...
The original power room was pretty useless. I want to build a new bath with a roll-in shower & linear drain. The laundry was relocated to an upper level but I want to anticipate putting in a stackable washer/dryer in the new bathroom. Two furnaces were put side-by-side in the basement. They are loud and I need to enclose them.
The construction that supported the first renovation pretty much used the basement without much thought. One result is that the DWV and supply lines for the floor above consumed a lot of head room that I would like to get back. I also need to relocate the water heater to put a water softener in where I want it.
Right now, I'm just planning things out. I think I have a workable plan, but that remains to be seen. I need to do some prep work first to get things situated better before any real construction can begin.
So ... I will have a bunch of questions ...
To start this off, I want to upload some design pictures and then deal with a couple specific DWV rework efforts to help me get my head room back in the proposed location for the new bath.
Here's what the basement looks like now and my proposed designs.
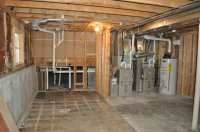
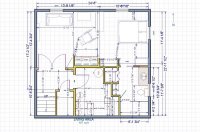
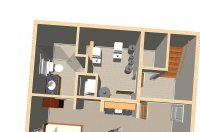
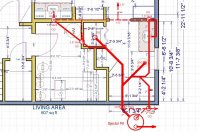
Here is the first question on re-working the DWV ... Can I move the drain pipe for the upstairs bathroom that runs overhead, across & under the joists? I want to route it so it ties into another stack that is next to the furnace. Please see these photos in the next post ...