A common rule of thumb for short cycling are burns shorter than 5 minutes, more than 5 burns per hour. At 5 minutes into the burn the average efficiency will usually be within 1% of the steady state efficiency, after discounting for flue purge and ignition cycle losses. At 10 minutes it's within a tiny fraction of a percent.
With higher frequency of ignition cycles the wear & tear goes up, ignition components fail, etc. There's no magic to the number 5- fewer is always better, but 5 burns in an hour with an average length of 6 minutes is a heluva lot easier the equipment and more efficient than 10 burns averaging 3 minutes, which is the same overall duty-cycle.
A differential swing of 30F below 145F isn't necessarily a problem, but can be depending on how long it takes the return water to get north of 130F. This boiler can take the thermal shock of cooler return water, but if it's chronically spending 75%+ of the burn times at temps below 130F it's likely to be a problem. A system bypass branch with a thermostatic mixing valve set to mix direct boiler output into the return water stream whenever the entering water temp drops below 130-135 F can help avoid that. A cheaper approach is to put a ball valve on the branch and hand-tweak it, but with an outdoor reset control that isn't going to work as well as a thermostatic mixing valve.
One approach to a system bypass looks like this:
The tee at the bottom just ahead of the pump would be where the thermostatic mixer goes, and the balance valve goes away. With the thermostatic control when ever the entering water temp at the pump is below the valve's setpoint there it reduces the return flow from the system, takes more flow from the bypass branch directly from the boiler's output. When the return water is eventually above the valve's setpoint it closes off the bypass branch completely.
Take a look at (or even a picture of) the near boiler plumbing, see what if any bypass measures were installed, just in case it needs to be tweaked.
With higher frequency of ignition cycles the wear & tear goes up, ignition components fail, etc. There's no magic to the number 5- fewer is always better, but 5 burns in an hour with an average length of 6 minutes is a heluva lot easier the equipment and more efficient than 10 burns averaging 3 minutes, which is the same overall duty-cycle.
A differential swing of 30F below 145F isn't necessarily a problem, but can be depending on how long it takes the return water to get north of 130F. This boiler can take the thermal shock of cooler return water, but if it's chronically spending 75%+ of the burn times at temps below 130F it's likely to be a problem. A system bypass branch with a thermostatic mixing valve set to mix direct boiler output into the return water stream whenever the entering water temp drops below 130-135 F can help avoid that. A cheaper approach is to put a ball valve on the branch and hand-tweak it, but with an outdoor reset control that isn't going to work as well as a thermostatic mixing valve.
One approach to a system bypass looks like this:
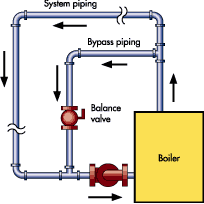
The tee at the bottom just ahead of the pump would be where the thermostatic mixer goes, and the balance valve goes away. With the thermostatic control when ever the entering water temp at the pump is below the valve's setpoint there it reduces the return flow from the system, takes more flow from the bypass branch directly from the boiler's output. When the return water is eventually above the valve's setpoint it closes off the bypass branch completely.
Take a look at (or even a picture of) the near boiler plumbing, see what if any bypass measures were installed, just in case it needs to be tweaked.