Smunderdog
New Member
Getting ready to put foam insulation down on the floor and up on the walls of my basement. I've read through all the other great forum posts but didn't see this addressed. 1957 ranch with a full basement. Previous owners had a perimeter floor drain installed that takes care of the ground water when things get soggy outside - basement stays nice and dry
So what is the best way to address the floor/wall interface with the foam board insulation? Take the 1" foam board right up to the drain and then drop the 2" foam board down the wall right to it completely covering the drain? Or should I stop the 2" insulation short and leave a small gap so ater can get into the drain should we ever have a flood type event in the basement?
I plan on using 7/16" T&G OSB on top of the 1" insulation as the subfloor. Once that is down I'll build the 2x4 perimeter walls on the OSB, put fiberglass insulation between the studs and drywall.
So what is the best way to address the floor/wall interface with the foam board insulation? Take the 1" foam board right up to the drain and then drop the 2" foam board down the wall right to it completely covering the drain? Or should I stop the 2" insulation short and leave a small gap so ater can get into the drain should we ever have a flood type event in the basement?
I plan on using 7/16" T&G OSB on top of the 1" insulation as the subfloor. Once that is down I'll build the 2x4 perimeter walls on the OSB, put fiberglass insulation between the studs and drywall.
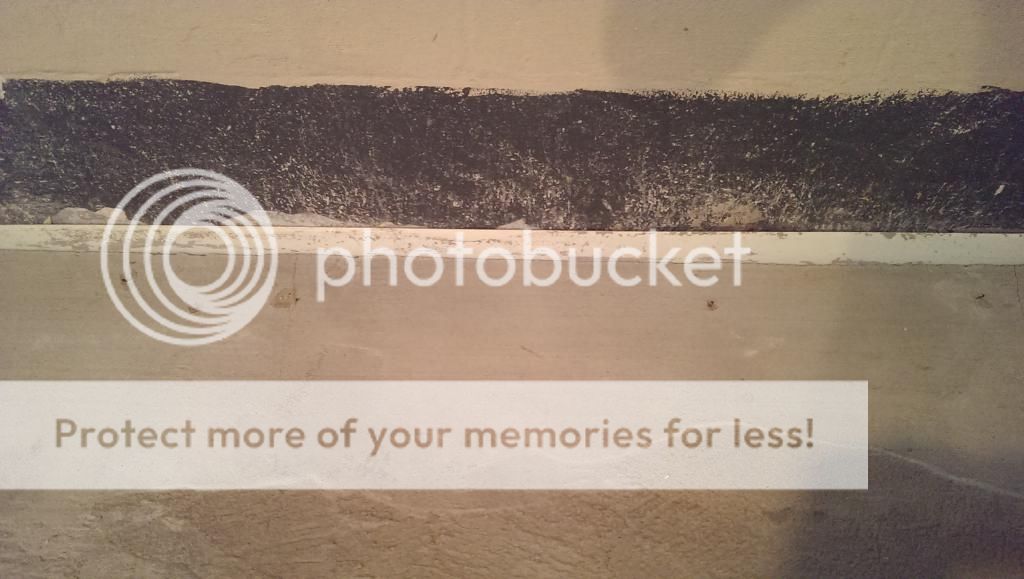
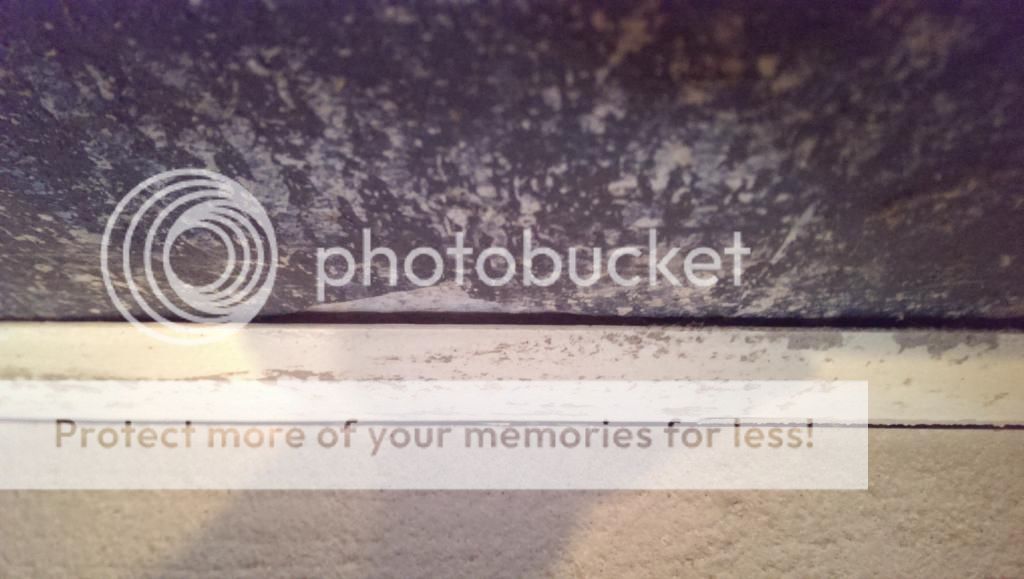