Hi and thanks.
Been having a tough time soldering an elbow to a main waste pipe, Newb here, first time with the torch. project is a faucet and pop up drain replacement. A corroded elbow pipe broke fro ma main waste line.
So i pulled out the corroded pip (bathroom sink), ground out the remnants of the old pipe (thin tinny metal) and roughed up the new cut elbow. I'm using silver solder (BenzOmatic kit from HD) and after using the whole roll i got some to stick but can't get the bottom. i have no room to work as the larger lead type thick pipe in the wall does not stick out. Also there is a tiny gap around the pipe I'm putting in.
Long story short i wonder if this is the right process for these metals, do i need plumbers putty and another type of solder (old setup had a dark grey welded look to it). I'm stuck as this waste line is connected to the master back so there is a bit of a drip when the master sink empties. Maybe I open the wall up and use a rubber connector here bet. the two pipes. Soldering iron vs torch?
Help and hope the pics tell a better story.
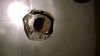
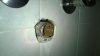
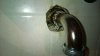
Been having a tough time soldering an elbow to a main waste pipe, Newb here, first time with the torch. project is a faucet and pop up drain replacement. A corroded elbow pipe broke fro ma main waste line.
So i pulled out the corroded pip (bathroom sink), ground out the remnants of the old pipe (thin tinny metal) and roughed up the new cut elbow. I'm using silver solder (BenzOmatic kit from HD) and after using the whole roll i got some to stick but can't get the bottom. i have no room to work as the larger lead type thick pipe in the wall does not stick out. Also there is a tiny gap around the pipe I'm putting in.
Long story short i wonder if this is the right process for these metals, do i need plumbers putty and another type of solder (old setup had a dark grey welded look to it). I'm stuck as this waste line is connected to the master back so there is a bit of a drip when the master sink empties. Maybe I open the wall up and use a rubber connector here bet. the two pipes. Soldering iron vs torch?
Help and hope the pics tell a better story.
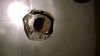
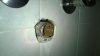
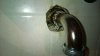